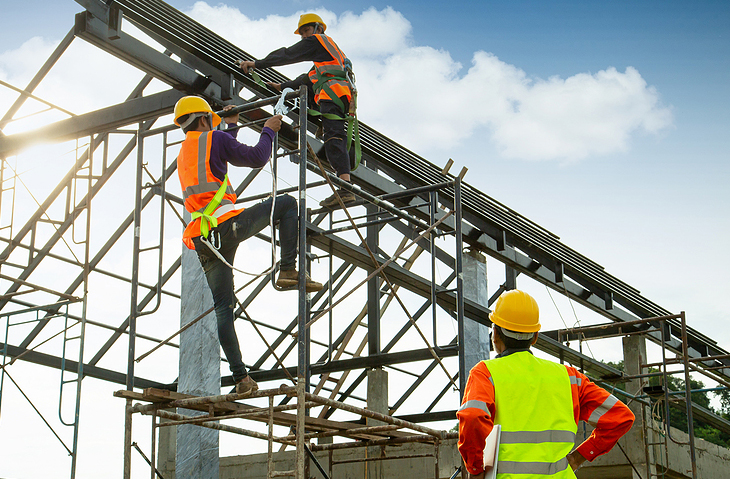
Structural and reinforcing iron and metal workers place and install iron or steel girders, columns, and other construction materials to form buildings, bridges, and other structures. They also position and secure steel bars or mesh in concrete forms in order to reinforce the concrete used in highways, buildings, bridges, tunnels, and other structures. In addition, they repair and renovate older buildings and structures. Even though the primary metal involved in this work is steel, these workers often are known as ironworkers or erectors. Some ironworkers make structural metal in fabricating shops, which are usually located away from the construction site.
Before construction can begin, ironworkers must erect steel frames and assemble the cranes and derricks that move structural steel, reinforcing bars, buckets of concrete, lumber, and other materials and equipment around the construction site. Once this job has been completed, workers begin to connect steel columns, beams, and girders according to blueprints and instructions from supervisors and superintendents. Structural steel, reinforcing rods, and ornamental iron generally come to the construction site ready for erection—cut to the proper size, with holes drilled for bolts and numbered for assembly.
Ironworkers at the construction site unload and stack the prefabricated steel so that it can be hoisted easily when needed. To hoist the steel, ironworkers attach cables (slings) to the steel and to the crane or derrick. One worker directs the hoist operator with hand signals while another worker holds a rope (tag line) attached to the steel to prevent it from swinging. The crane or derrick hoists steel into place in the framework, whereupon two ironworkers, called connectors, position the steel with connecting bars and spud wrenches—a long wrench with a pointed handle. Workers using driftpins or the handle of a spud wrench align the holes in the steel with the holes in the framework. Ironworkers check vertical and horizontal alignment with plumb bobs, laser equipment, transits, or levels; then they bolt or weld the piece permanently in place.
Reinforcing iron and rebar workers, sometimes called rod busters, set reinforcing bars (often called rebar) in the forms that hold concrete, following blueprints showing the location, size, and number of bars. They then fasten the bars together by tying wire around them with pliers. When reinforcing floors, ironworkers place spacers under the rebar to hold the bars off the deck. Although these materials usually arrive ready to use, ironworkers occasionally must cut bars with metal shears or acetylene torches, bend them by hand or machine, or weld them with arc-welding equipment. Some concrete is reinforced with welded wire fabric that ironworkers put into position using hooked rods. Post-tensioning is another technique used to reinforce concrete. In this technique, workers substitute cables for rebar. When the concrete is poured, the ends of the cables are left exposed. After the concrete cures, ironworkers tighten the cables with jacking equipment specially designed for the purpose. Post-tensioning allows designers to create larger open areas in a building, because supports can be placed further apart. This technique is commonly employed in parking garages and arenas.
Ornamental ironworkers install stairs, handrails, curtain walls (the nonstructural walls and window frames of many large buildings), and other miscellaneous metal after the structure of the building has been completed. As they hoist pieces into position, ornamental ironworkers make sure that the pieces are properly fitted and aligned before bolting or welding them for a secure fit.
Work Environment
Structural and reinforcing iron and metal workers usually work outside in all kinds of weather. However, those who work at great heights do not work during wet, icy, or extremely windy conditions. Because the danger of injuries from falls is great, ironworkers use safety devices such as safety harnesses, scaffolding, and nets to reduce risk. Nevertheless, this occupation does experience an above average rate of nonfatal injuries.
Education & Training Required
Most employers recommend a 3-year to 4-year apprenticeship consisting of a combination of paid on-the-job training and classroom instruction as the best way to learn this trade. Apprenticeship programs are administered by committees made up of representatives of local unions of the International Association of Bridge, Structural, Ornamental and Reinforcing Iron Workers or the local chapters of contractors' associations. To be accepted into an apprenticeship program, most employers and local apprenticeship committees prefer that applicants have a high school diploma. In addition, high school courses in general mathematics, mechanical drawing, English, and welding are considered helpful.
Classroom study for apprentices consists of blueprint reading; mathematics, the basics of structural erecting, rigging, reinforcing, welding, assembling, and safety training. Apprentices also study the care and safe use of tools and materials. On the job, apprentices work in all aspects of the trade, such as unloading and storing materials at the job site, rigging materials for movement by crane, connecting structural steel, and welding.
Some ironworkers learn the trade informally on the job, without completing an apprenticeship. On-the-job trainees usually begin by assisting experienced ironworkers on simple jobs, such as carrying various materials. With experience, trainees perform more difficult tasks, such as cutting and fitting different parts.
Other Skills Required
Ironworkers must be at least 18 years old. Because materials used in iron working are heavy and bulky, ironworkers must be in good physical condition. They also need good agility, balance, eyesight, and depth perception to work safely at great heights on narrow beams and girders. Ironworkers should not be afraid of heights or suffer from dizziness.
How to Advance
Ironworkers who complete apprenticeships are certified at the journey level, which often make them more competitive candidates for jobs and promotions. Those who meet education and experience requirements can become welders certified by the American Welding Society. Apprenticeship programs often provide trainees the opportunity to become welder-certified as part of their coursework because welding skills are useful for many ironworker tasks.
Some experienced workers are promoted to supervisor. Others may go into the contracting business for themselves. The ability to communicate in both English and Spanish will improve opportunities for advancement.
Job Outlook
Average job growth is projected. In most areas of the country, job opportunities should be favorable.
Earnings
Median hourly wages of structural iron and steel workers is $30.68. The middle 50 percent earned between $25.18 and $39.15. The lowest 10 percent earned less than $22.25, and the highest 10 percent earned more than $47.04.
Median hourly wages of reinforcing iron and rebar workers is $29.18. The middle 50 percent earned between $24.35 and $36.29. The lowest 10 percent earned less than $21.78, and the highest 10 percent earned more than $45.26.
Median hourly wages of structural iron and steel workers in foundation, structure, and building exterior contractors is $31.51 and in nonresidential building construction, $28.53. Reinforcing iron and rebar workers earned median hourly wages of $24.37 in foundation, structure, and building exterior contractors. About 40 percent of the workers in this trade are union members. According to International Association of Bridge, Structural, Ornamental, and Reinforcing Iron Workers, average hourly compensation, including benefits, for structural and reinforcing metal workers who belonged to a union and worked full time were higher than the hourly earnings of nonunion workers.
Structural and reinforcing iron and metal workers in New York, Boston, San Francisco, Chicago, Los Angeles, Philadelphia, and other large cities received the highest wages. Apprentices generally start at about 60 percent of the rate paid to experienced journey level workers. Throughout the course of the apprenticeship program, as they acquire skills they receive periodic increases until their pay approaches that of experienced workers. Earnings for ironworkers may be reduced on occasion because work can be limited by bad weather and economic downturns.