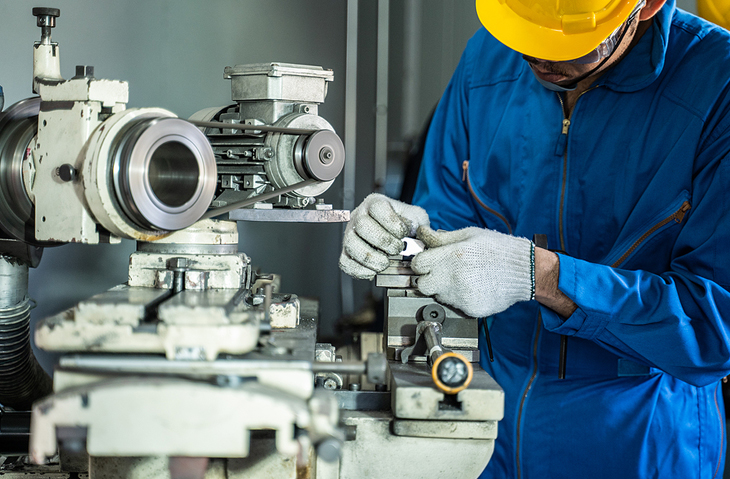
Imagine an automobile assembly line: a large conveyor system moves unfinished automobiles down the line, giant robotic welding arms bond the different body panels together, hydraulic lifts move the motor into the body of the car, and giant presses stamp body parts from flat sheets of steel. All these complex machines need workers to install them and service them to make sure they function properly. Assembling and setting up these machines on the factory floor is the job of millwrights, while industrial machinery mechanics and machinery maintenance workers maintain and repair these machines.
Millwrights are the highly skilled workers who install, assemble, and, when necessary, dismantle machinery in factories, power plants, and construction sites. These workers consult with engineers and managers to determine the best location to place a machine. Millwrights then transport the machine parts to the desired location, using fork lifts, hoists, winches, cranes and other equipment. Machines do not arrive in one piece, and millwrights need to assemble them from their component parts. Millwrights must understand how a machine functions to assemble and disassemble it properly; this may involve knowledge of electronics, pneumatics, and computer systems. They use complex instruction books that detail the assembly of the machinery and use tools such as levels, welding machines, and hydraulic torque wrenches. Millwrights use micrometers, precision measuring devices, to achieve the extreme tolerances required by modern machines. On large projects, the use of cranes and trucks is common.
Assembly of a machine can take a few days or several weeks. Aside from assembly, millwrights are also involved in major repairs and disassembly of machines. If a manufacturing plant needs to clear floor space for new machinery, it can sell or trade-in old equipment. The breaking down of a machine is normally just as complicated as assembling it; all parts must be carefully taken apart, categorized and packaged for shipping.
While major repairs may require the assistance of a millwright, keeping machines in good working order is the primary responsibility of industrial machinery mechanics, also called industrial machinery repairers or maintenance machinists. To do this effectively, these workers must be able to detect minor problems and correct them before they become larger problems. Machinery mechanics use technical manuals, their understanding of the equipment, and careful observation to discover the cause of the problem. For example, after hearing a vibration from a machine, the mechanic must decide whether it is due to worn belts, weak motor bearings, or some other problem. Mechanics often need years of training and experience to fully diagnose all problems, but computerized diagnostic systems and vibration analysis techniques provide aid in determining the nature of the problem.
After diagnosing the problem, the industrial machinery mechanic may disassemble the equipment to repair or replace the necessary parts. Increasingly, mechanics are expected to have the electrical, electronics, and computer programming skills to repair sophisticated equipment on their own. Once a repair is made, mechanics perform tests to ensure that the machine is running smoothly. Primary responsibilities of industrial machinery mechanics also include preventive maintenance; for example, they adjust and calibrate automated manufacturing equipment, such as industrial robots.
The most basic maintenance and repair tasks are performed by machinery maintenance workers. These employees are responsible for cleaning and lubricating machinery, performing basic diagnostic tests, checking performance, and testing damaged machine parts to determine whether major repairs are necessary. In carrying out these tasks, maintenance workers must follow machine specifications and adhere to maintenance schedules. Maintenance workers may perform minor repairs, but major repairs generally are left to machinery mechanics.
Industrial machinery mechanics and machinery maintenance workers use a variety of tools to perform repairs and preventive maintenance. They may use handtools to adjust a motor or a chain hoist to lift a heavy printing press off the ground. When replacements for broken or defective parts are not readily available, or when a machine must be returned quickly to production, mechanics may create a new part using lathes, grinders, or drill presses. Mechanics use catalogs to order replacement parts and often follow blueprints, technical manuals, and engineering specifications to maintain and fix equipment. By keeping complete and up-to-date records, mechanics try to anticipate trouble and service equipment before factory production is interrupted. If an industrial machinery mechanic is unable to repair a machine and a major overhaul is needed, a millwright with expertise on the machine may be hired to make the repair.
Work Environment
Industrial machinery mechanics, machinery maintenance workers, and millwrights held about 501,500 jobs in 2020. Employment in the detailed occupations that make up industrial machinery mechanics, machinery maintenance workers, and millwrights was distributed as follows:
- Industrial machinery mechanics - 391,800
- Maintenance workers, machinery - 65,600
- Millwrights - 44,200
The largest employers of industrial machinery mechanics, machinery maintenance workers, and millwrights were as follows:
- Manufacturing - 54%
- Wholesale trade - 11%
- Commercial and industrial machinery and equipment (except automotive and electronic) repair and maintenance - 10%
- Construction - 7%
Injuries and Illnesses
Working with industrial machinery can be dangerous. To avoid injury, workers must follow safety precautions and use protective equipment, such as hardhats, safety glasses, steel-toed shoes, gloves, and earplugs.
Work Schedules
Most industrial machinery mechanics and machinery maintenance workers are employed full time during regular business hours. However, mechanics may be on call and work night or weekend shifts. Overtime is common, particularly for mechanics.
Education & Training Required
All machinery maintenance and millwright worker positions generally require a high school diploma, GED, or its equivalent. However, employers increasingly prefer to hire machinery maintenance workers with some training in industrial technology. Employers also prefer to hire those who have taken high school or postsecondary courses in mechanical drawing, mathematics, blueprint reading, computer programming, or electronics.
Most millwrights, and some industrial machinery mechanics, enter the occupation through an apprenticeship program that typically lasts about 4 years. Apprenticeships can be sponsored by local union chapters, employers, or the State labor department. Training in these apprenticeships involves a combination of on-the-job training and classroom learning. Jobseekers can apply for union apprenticeships, and qualified applicants may begin training in local training facilities and factories.
Industrial machinery mechanics usually need a year or more of formal education and training after high school to learn the growing range of mechanical and technical skills that they need. While mechanics used to specialize in one area, such as hydraulics or electronics, many factories now require every mechanic to have knowledge of electricity, electronics, hydraulics, and computer programming.
Workers can get this training in a number of different ways. A 2-year associate degree program in industrial maintenance provides good preparation. Other mechanics may start as helpers or in other factory jobs and learn the skills of the trade informally and by taking courses offered through their employer. It is common for experienced production workers to move into maintenance positions if they show good mechanical abilities. Employers may offer on-site classroom training or send workers to local technical schools while they receive on-the-job training. Classroom instruction focuses on subjects such as shop mathematics, blueprint reading, welding, electronics, and computer training. In addition to classroom training, it is important that mechanics train on the specific machines they will repair. They can get this training on the job, through dealer or manufacturer's representatives, or in a classroom.
Machinery maintenance workers typically receive on-the-job training lasting a few months to a year to perform routine tasks, such as setting up, cleaning, lubricating, and starting machinery. This training may be offered by experienced workers, professional trainers, or representatives of equipment manufacturers.
Other Skills Required
Machinery mechanics must have good problem-solving abilities, as it is important for them to be able to discover the cause of a problem to repair it. Mechanical aptitude and manual dexterity are also important. Good reading comprehension is necessary to understand the technical manuals of a wide range of machines; and good communications skills are also essential in order for millwrights, mechanics and maintenance workers to understand the needs of other workers and managers. In addition, good physical conditioning and agility are necessary because repairers sometimes have to lift heavy objects or climb to reach equipment.
How to Advance
Opportunities for advancement vary by specialty. Machinery maintenance workers, if they take classes and gain additional skills, may advance to industrial machinery mechanic or supervisor. Industrial machinery mechanics also advance by working with more complicated equipment and gaining additional repair skills. The most highly skilled repairers can be promoted to supervisor, master mechanic, or millwright. Experienced millwrights can advance into team leading roles.
Job Outlook
Overall employment of industrial machinery mechanics, machinery maintenance workers, and millwrights is projected to grow 19 percent from 2020 to 2030, much faster than the average for all occupations.
About 56,300 openings for industrial machinery mechanics, machinery maintenance workers, and millwrights are projected each year, on average, over the decade. Many of those openings are expected to result from the need to replace workers who transfer to different occupations or exit the labor force, such as to retire.
Employment
The continuing adoption of automated manufacturing machinery will require more maintenance workers, mechanics, and millwrights to keep machines in good working order over the next decade. The use of automated conveyors to move products and materials in factories is an area of high demand for these workers, because the conveyor belts, motors, and rollers need regular care and maintenance.
Earnings
The median annual wage for industrial machinery mechanics, machinery maintenance workers, and millwrights was $59,380 in May 2021. The median wage is the wage at which half the workers in an occupation earned more than that amount and half earned less. The lowest 10 percent earned less than $37,260, and the highest 10 percent earned more than $78,900.
Median annual wages for industrial machinery mechanics, machinery maintenance workers, and millwrights in May 2021 were as follows:
- Millwrights - $60,330
- Industrial machinery mechanics - $59,840
- Maintenance workers, machinery - $48,900
In May 2021, the median annual wages for industrial machinery mechanics, machinery maintenance workers, and millwrights in the top industries in which they worked were as follows:
- Manufacturing - $59,820
- Construction - $59,770
- Wholesale trade - $56,900
Commercial and industrial machinery and equipment (except automotive and electronic) repair and maintenance 48,270
Most industrial machinery mechanics and machinery maintenance workers are employed full time during regular business hours. However, mechanics may be on call or assigned to work night or weekend shifts. Overtime is common, particularly for mechanics.