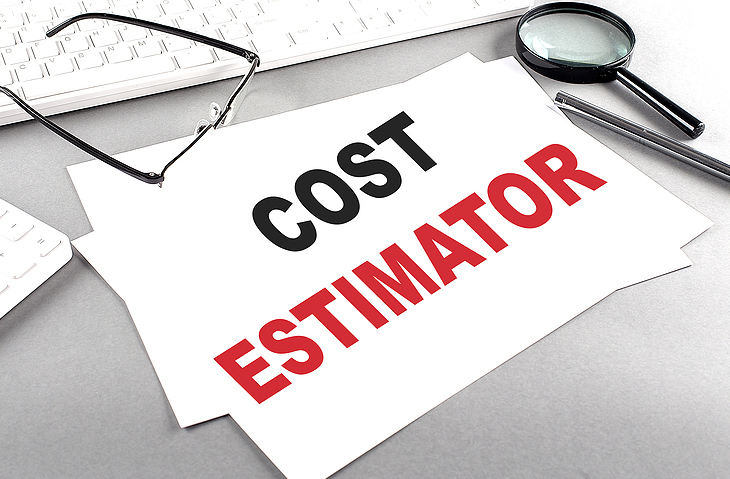
Accurately forecasting the cost, size, and duration of future projects is vital to the survival of any business. Cost estimators develop the cost information that business owners and managers need to make a bid for a contract or to decide on the profitability of a proposed new project or product. They also determine which endeavors are making a profit.
Regardless of the industry in which they work, estimators collect and analyze data on all of the factors that can affect costs, such as materials, labor, location, duration of the project, and special machinery requirements, including computer hardware and software. Job duties vary widely depending on the type and size of the project.
The methods for estimating costs can also differ greatly by industry. On a large construction project, for example, the estimating process begins with the decision to submit a bid. After reviewing various preliminary drawings and specifications, the estimator visits the site of the proposed project. The estimator gathers information on access to the site; surface topography and drainage, and the availability of electricity, water, and other services. The estimator records this information, which may go in the final project estimate.
After the site visit, the estimator determines the quantity of materials and the labor required to complete the firm’s part of the project. This process, called the quantity survey or “takeoff,” involves completing standard estimating forms, filling in dimensions, numbers of units, and other information. A cost estimator working for a general contractor, for example, estimates the costs of all of the items that the contractor must provide. Although subcontractors estimate their costs as part of their own bidding process, the general contractor's cost estimator often analyzes bids made by subcontractors. Also during the takeoff process, the estimator must make decisions concerning equipment needs, the sequence of operations, the size of the crew required, and physical constraints at the site. Allowances for wasted materials, inclement weather, shipping delays, and other factors that may increase costs also must be incorporated in the estimate.
After completing the quantity surveys, the estimator prepares a cost summary for the entire project, which includes the costs of labor, equipment, materials, subcontractors, overhead, taxes, insurance, markup, and any additional costs that may affect the project. The chief estimator then prepares the bid proposal for submission to the owner. On large construction projects, there may be several estimators, each specializing in one area, such as electrical work or excavation, concrete, and forms.
Construction cost estimators also may be employed by the project's architect, engineering firm, or owner to help establish a budget, manage and control project costs, and to track actual costs relative to bid specifications as the project develops. During construction, estimators may be employed to manage the cost of change orders and negotiate and settle and extra costs or mitigate potential claims. Estimators may also be called upon as expert witness on cost in a construction dispute case.
In manufacturing, cost estimators usually are assigned to the engineering, cost, or pricing department. The estimator's goal is to accurately estimate the costs associated with developing and producing products. The job may begin when management requests an estimate of the costs associated with a major redesign of an existing product or the development of a new product or production process. For example, when estimating the cost of manufacturing a new product, the estimator works with engineers, first reviewing blueprints or conceptual drawings to determine the machining operations, tools, gauges, and materials that will be required. The estimator then prepares a parts list and determines whether it would be more efficient to produce or to purchase the parts. To do this, the estimator asks for price information from potential suppliers. The next step is to determine the cost of manufacturing each component of the product. Some high-technology products require a considerable amount of computer programming during the design phase. The cost of software development is one of the fastest growing and most difficult activities to estimate. As a result, some cost estimators now specialize in estimating only computer software development and related costs.
Thereafter, the cost estimator prepares time-phase charts and learning curves. Time-phase charts indicate the time required for tool design and fabrication, tool “debugging”—finding and correcting all problems—manufacturing of parts, assembly, and testing. Learning curves graphically represent the rate at which the performance of workers producing parts for the new product improves with practice. These curves are commonly called “cost reduction” curves, because many problems—such as engineering changes, rework, shortages of parts, and lack of operator skills—diminish as the number of units produced increases, resulting in lower unit costs.
Using all of this information, the estimator then calculates the standard labor hours necessary to produce a specified number of units. Standard labor hours are then converted to dollar values, to which are added factors for waste, overhead, and profit to yield the unit cost in dollars. The estimator compares the cost of purchasing parts with the firm's estimated cost of manufacturing them to determine which is less expensive.
Computers play a vital role in cost estimation because the process often involves complex mathematical calculations and requires advanced mathematical techniques. For example, to undertake a parametric analysis (a process used to estimate costs per unit based on square footage or other specific requirements of a project), cost estimators use a computer database containing information on the costs and conditions of many other similar projects. Although computers cannot be used for the entire estimating process, they can relieve estimators of much of the drudgery associated with routine, repetitive, and time-consuming calculations. New and improved cost estimating software has lead to more efficient computations, leaving estimators more time to visit and analyze projects.
Operations research, production control, cost, and price analysts who work for government agencies may do significant amounts of cost estimating in the course of their usual duties. In addition, the duties of construction managers may include estimating costs.
Work Environment
Cost estimators held about 199,400 jobs in 2020. The largest employers of cost estimators were as follows:
- Specialty trade contractors - 36%
- Construction of buildings - 18%
- Manufacturing - 13%
- Automotive repair and maintenance - 7%
- Heavy and civil engineering construction - 6%
Cost estimators work mostly in office settings, and some estimators visit construction sites and factory assembly lines during the course of their work.
Work Schedules
Most cost estimators work full time, and some work more than 40 hours per week.
Education & Training Required
In the construction industry, employers increasingly prefer individuals with a degree in construction management, building science, or construction science, all of which usually include several courses in cost estimating. Most construction estimators also have considerable construction experience, gained through work in the industry, internships, or cooperative education programs; and for some estimators, years of experience can substitute for a degree in addition to taking classes in the field or getting an associate degree. Applicants with a thorough knowledge of construction materials, costs, and procedures in areas ranging from heavy construction to electrical work, plumbing systems, or masonry work have a competitive edge.
In manufacturing industries, employers prefer to hire individuals with a degree in engineering, physical science, operations research, mathematics, or statistics or in accounting, finance, business, economics, or a related subject. In most industries, experience in quantitative techniques is important.
Many colleges and universities include cost estimating as part of bachelor's and associate degree curriculums in civil engineering, industrial engineering, information systems development, and construction management or construction engineering technology. In addition, cost estimating is often part of master's degree programs in construction science or construction management. Organizations representing cost estimators, such as the American Society of Professional Estimators (ASPE), the Association for the Advancement of Cost Engineering (AACE International) and the Society of Cost Estimating and Analysis (SCEA), also sponsor educational and professional development programs. These programs help students, estimators-in-training, and experienced estimators learn about changes affecting the profession. Specialized courses and programs in cost-estimating techniques and procedures also are offered by many technical schools, community colleges, and universities.
Estimators also receive long-term training on the job because every company has its own way of handling estimates. Working with an experienced estimator, newcomers become familiar with each step in the process. Those with no experience reading construction specifications or blueprints first learn that aspect of the work. Subsequently, they may accompany an experienced estimator to the construction site or shop floor, where they observe the work being done, take measurements, or perform other routine tasks. As they become more knowledgeable, estimators learn how to tabulate quantities and dimensions from drawings and how to select the appropriate prices for materials.
Other Skills Required
Cost estimators need to have an aptitude for mathematics, be able to analyze, compare, and interpret detailed but sometimes poorly defined information, and be able to make sound and accurate judgments based on this information. The ability to focus on details, while analyzing and managing larger obstacles, is vital. Assertiveness and self-assurance in presenting and supporting conclusions are also important, as are strong communications and interpersonal skills, because estimators may work as part of a team alongside managers, owners, engineers, and design professionals. Cost estimators also need to be proficient with computers and have skills in programming. Familiarity with cost estimation software, including commercial, and Building Information Modeling (BIM) software is beneficial. BIM software technology takes standard blueprints and creates three-dimensional models on the computer, allowing for better estimates of the building process. Proficiency in project management and the ability to incorporate work breakdown structure (WBS) techniques are increasingly important in cost estimating complex development projects.
How to Advance
Voluntary certification can be beneficial to cost estimators because it provides professional recognition of the estimator's competence and experience. In some instances, individual employers may even require professional certification for employment. The ASPE, AACE International, and SCEA administer certification programs. To become certified, estimators usually must have between 2 and 8 years of estimating experience and must pass a written examination. In addition, certification requirements may include the publication of at least one article or paper in the field.
For most estimators, advancement takes the form of higher pay and prestige. Some move into management positions, such as project manager for a construction firm, program manager for a government contractor, or manager of the industrial engineering department for a manufacturer. Others may go into business for themselves as consultants, providing estimating services for a fee to government or to construction or manufacturing firms.
Job Outlook
Employment of cost estimators is projected to show little or no change from 2020 to 2030.
Despite limited employment growth, about 17,800 openings for cost estimators are projected each year, on average, over the decade. Most of those openings are expected to result from the need to replace workers who transfer to different occupations or exit the labor force, such as to retire.
Employment
There will continue to be some demand for cost estimators because companies need accurate cost projections to ensure that their products and services are profitable.
However, cost estimation software is improving the productivity of these workers, requiring fewer estimators to do the same amount of work. This will limit employment demand for cost estimators.
Earnings
The median annual wage for cost estimators was $65,170 in May 2021. The median wage is the wage at which half the workers in an occupation earned more than that amount and half earned less. The lowest 10 percent earned less than $38,880, and the highest 10 percent earned more than $115,690.
In May 2021, the median annual wages for cost estimators in the top industries in which they worked were as follows:
- Heavy and civil engineering construction - $80,510
- Construction of buildings - $76,450
- Specialty trade contractors - $69,200
- Manufacturing - $62,570
- Automotive repair and maintenance - $60,420
Most cost estimators work full time, and some work more than 40 hours per week.