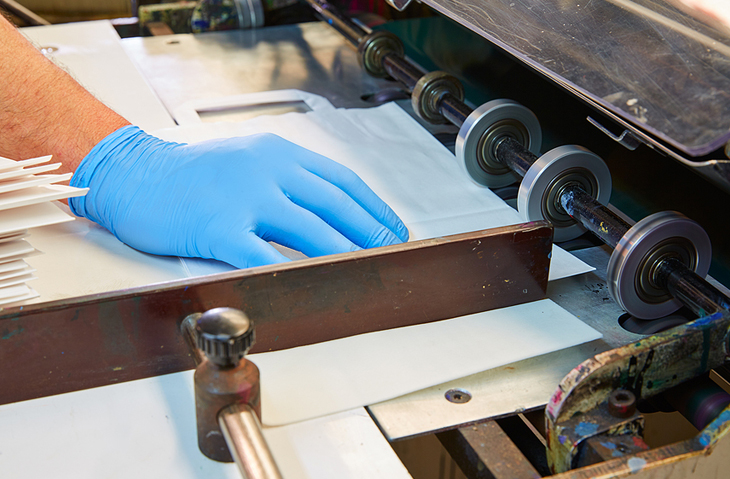
The printing process has three stages: prepress, press, and binding or finishing. While workers in small print shops are usually responsible for all three stages, in most printing firms, formatting print jobs and correcting layout errors before the job goes to print is the responsibility of a specialized group of workers. Prepress technicians and workers are responsible for this prepress work. They perform a variety of tasks to help transform text and pictures into finished pages and prepare the pages for print.
Some prepress technicians, known as “preflight technicians,” take images from graphic designers, customer service staff, team leaders, or directly from customers and check them for completeness. They review job specifications and design either from submitted sketches or clients’ electronic files to ensure that everything is correct and all files and photos are included. Once clients and preflight technicians agree that everything is in order, preflight technicians forward the files to prepress technicians to set up printers.
Offset printing plates are thin sheets of metal that carry the final image to be printed. Printing presses use this plate to copy the image to the final printed products. Once a printing plate has been created, prepress technicians collaborate with printing press operators to check for any potential printing problems. Several plates may be needed if a job requires color, but advanced printing technology generally does not require plates.
Prepress workers generally use a photographic process to make offset printing plates. This is a complex process involving ultraviolet light and chemical exposure through which the text and images of a print job harden on a metal plate and become water repellent. These hard, water repellent portions of the metal plate are in the form of the text and images that will be printed. More recently, however, the printing industry has moved to technology known as “direct-to-plate,” by which the prepress technicians send the data directly to a plating system, bypassing the need for the photographic technique. The direct-to-plate technique is just one example of digital imaging technology that has largely replaced cold-type print technology.
Using direct-to-plate technology, the technicians produce an electronic image of the printed pages. The electronic image is used to create a “proof” which is printed and delivered or mailed to the customer. Alternatively, the electronic file can be e-mailed to the client for a final check. Once the customer approves the proofs, technicians use laser “imagesetters” to expose digital images of the pages directly onto the thin metal printing plates or directly to a digital press and skip the plate-making process altogether.
Advances in computer software and printing technology continue to change prepress work. Prepress workers often receive files from customers on a computer disk, via e-mail, or through an Internet site that contains typeset material already laid out in pages. This work is usually done by desktop publishers or graphic designers who have knowledge of publishing software. Despite the shortcuts that technological advancements allow, workers still need to understand the basic processes behind prepress, press, and finishing operations. Some workers, known as job printers, perform prepress and print operations. Job printers often are found in small establishments where work combines several job skills.
Work Environment
Prepress technicians and workers usually work in clean, air-conditioned areas with little noise. Some workers may develop eyestrain from working in front of a video display terminal or other problems, such as muscle aches or back pain. Workers are often subject to stress and the pressures of deadlines and tight work schedules. Prepress employees usually work an 8-hour day. Some workers—particularly those employed by newspapers—work night shifts. Weekend and holiday work may be required, particularly when a print job is behind schedule. Part-time job printers and prepress technicians made up about 14 percent of this occupation.
Education & Training Required
Many employers consider the best candidates for prepress jobs to be individuals with a combination of work experience in the printing industry and formal training in new digital technology. The experience of these applicants provides them with an understanding of how printing plants operate and demonstrates their interest in advancing within the industry.
Traditionally, prepress technicians and workers started as helpers and were trained on the job. Some of these jobs required years of experience performing detailed manual work to become skillful enough to perform the most difficult tasks. Today, however, employers expect workers to have some formal postsecondary graphic communications training in the various types of computer software used in digital imaging and will train workers on the job as needed.
For beginners, 2-year associate degree programs offered by community colleges, junior colleges, and technical schools teach the latest prepress skills and allow students to practice applying them. There are also 4-year bachelor's degree programs in graphic design aimed primarily at students who plan to move into management positions in printing or design. For workers who do not wish to enroll in a degree program, prepress-related courses are offered at many community colleges, junior colleges, 4-year colleges and universities, vocational-technical institutes, and private trade and technical schools. Workers with experience in other printing techniques can take a few college-level graphic communications courses to upgrade their skills and qualify for prepress jobs.
Other Skills Required
Employers prefer workers with good communication skills, both oral and written. When prepress problems arise, prepress technicians should be able to deal courteously with customers to resolve them. In small shops, they may take customer orders and provide pricing information. Persons interested in working for firms using advanced printing technology need to be comfortable with electronics and computers. At times, prepress personnel may have to perform computations in order to estimate job costs or operate many of the machines used to run modern printing equipment.
Prepress technicians and workers need manual dexterity and accurate eyesight. Good color vision helps workers find mistakes and locate potential problems. It is essential for prepress workers to be able to pay attention to detail and work independently. Artistic ability is often a plus. Employers also seek persons who are comfortable with the pressures of meeting deadlines, using new software, and operating new equipment.
How to Advance
Employers may send experienced technicians to industry-sponsored programs to update or develop new skills. Retraining due to technology and equipment changes is a constant as printing firms continually seek ways to improve efficiency and lower production costs. This kind of prepress training is sometimes offered in-house or through equipment makers and unions in the printing industry.
Job Outlook
Employment of prepress technicians and workers is projected to decline because of improvements in printing technology that require fewer of these workers. Despite this, job prospects are good for prepress technicians with good computer and customer service skills.