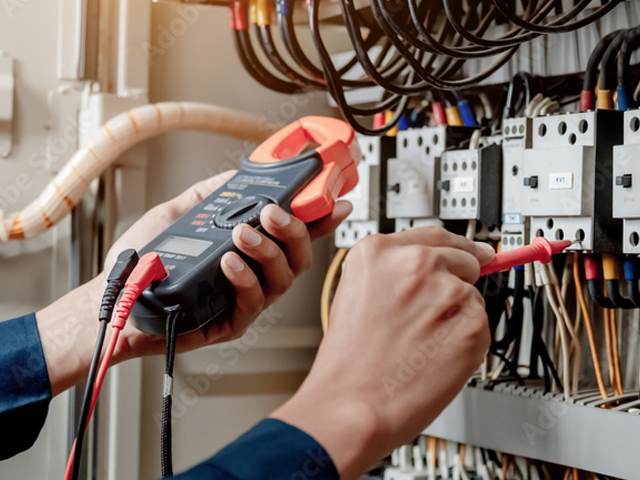
In Australia, the term "test and tag" refers to a critical safety practice aimed at ensuring electrical appliances and equipment are safe to use in various settings. This procedure plays a pivotal role in preventing electrical hazards, fire risks, and other safety concerns associated with the use of electrical devices.
The Test and tag process is particularly important in workplaces, schools, public facilities, and other locations where electrical appliances are in regular use. Test and tag course trainers, Get Skilled, provides more detail of this procedure.
What’s involved in Test & Tag?
The test and tag procedure comprises two essential steps: initially conducting a visual examination to identify any damage, and subsequently subjecting the appliance to electrical testing using a Portable Appliance Tester.
Once these two steps are complete including the item testing, it is affixed with a tag that serves to confirm its testing status. This tag displays pertinent information, including the identity of the individual who conducted the test, the date of the test, and the scheduled date for the next test.
The primary objective of the testing and tagging process is to ensure the safety of individuals within the workplace who interact with these appliances, all the while mitigating the potential for electrical hazards. In the unfortunate event of an accident occurring with an appliance that has not been subjected to prior testing and tagging, the responsibility may fall upon the employer.
The Australian Standard
AS/NZS 3760 is the Australian standard that governs test and tag. It offers comprehensive guidance and regulations about electrical safety within the industry itself. Further, it outlines recommendations for test and tag intervals, as well as what qualified personnel are authorised to perform testing and tagging.
This Standard was recently updated in 2022 and therefore, is now known as the AS/NZS 3760:2022, reflecting various amendments and enhancements.
What Industries Require Test and Tag
In certain heavy-duty industries like construction, demolition, and mining, the rigorous demands of the job necessitate a strict testing and tagging schedule, with appliances requiring assessment every three months.
This heightened frequency of testing is primarily due to the unforgiving nature of these industries, where equipment tends to endure more wear and tear.
To ensure clarity and effectiveness in this process, the test and tag colours change at different intervals throughout the year, aligning specific months with designated test tag colours.
In contrast, for most other workplaces, testing and tagging is not mandated by law. However, employers carry a legal duty of care towards their employees, which means they are responsible for ensuring the safety of their workforce.
If an accident were to occur involving an appliance that hadn't been tested and proved to be unsafe, the employer could potentially face liability.
For individuals in the hiring industry, there are specific minimum requirements in place. Before renting out equipment, a hirer must conduct a visual inspection to verify its condition.
Additionally, while the equipment is in their possession, the hirer must perform electrical testing every three months to maintain safety standards and compliance.
Who is Qualified to Test and Tag
Many think only electricians can test and tag however that is not true. According to AS/NZS 3760:2022, test and tag can be conducted by someone who is considered a ‘Competent Person’. This will usually be someone who has undertaken test and tag training to acquire the knowledge to be competent with the skills and learn the equipment required in this process.
What Types of Items Are Tested and Tagged?
Any device with a flexible cable, a detachable plug, and operating at voltages higher than 50V are the types of items tested and tagged.
Electric appliances are typically classified into two categories:
- Class I - These are grounded appliances, such as kettles, irons, and toasters.
- Class II - These are double-insulated appliances, often identifiable by a symbol (a square within a square) or the words 'Double Insulated.' Examples include most electric drills and hair dryers.
It's important to note that newly acquired equipment doesn't require full-scale testing; a visual inspection and tagging are sufficient.
How Often Should These Items Be Tested and Tagged?
The Australian Standard provides specific guidelines for test and tag frequencies, which are determined by the specific environment in which the appliance is used. These recommendations are outlined in the AS 3760 Standard through 'Table 2.4,' which specifies the minimum requirements. However, in some cases, these frequencies may vary based on an individual workplace's risk assessment.
For instance, construction sites typically require testing every 3 months, while factories or warehouses may have a 6-month testing frequency.